До настоящего времени в нашей стране преобладающее количество стали массового назначения, в том числе низколегированной.
На металлургических заводах, не имеющих в своем составе доменного производства, а также на машиностроительных заводах со сталеплавильным и прокатным производством низколегированную сталь выплавляют скрап-процессом на твердом чугуне.
По мере повышения доли конвертерной стали в общем объеме производства возрастает роль этого способа получения стали и в производстве низколегированной стали. Процесс выплавки стали должен быть организован таким образом, чтобы обеспечить получение стали высокого качества с наименьшим количеством неметаллических включений. Для этого должны быть созданы условия, обеспечивающие получение хорошо прокипевшего металла, с минимальным содержанием газов и вредных примесей (серы, фосфора).
Длительное время считалось, что качественную сталь, в том числе и низколегированную, следует выплавлять исключительно в печах небольшого тонна ка и что с увеличением объема печи качество стали снижается. Однако внедрение в практику сталеплавильного производства основных хромомагнезитовых сводов, обогащение факела и продувка ванны кислородом (или компрессорным воздухом) позволили интенсифицировать процесс, проводить мартеновскую плавку на высоком температурном режиме и ускорить шлакообразование. Этим созданы необходимые условия для успешной выплавки низколегированной стали в большегрузных мартеновских печах практически любого тоннажа. Лишь отдельные марки, наиболее сложные по составу и с низким содержанием углерода при высоком содержании марганца, предпочтительней выплавлять в одножелобных печах (до 300 т). Низколегированную сталь можно выплавлять только в печах, обеспечивающих быстрое расплавление шихты, интенсивное шлакообразование и окисление углерода, а также хороший нагрев металла к моменту его выпуска.
После горячего ремонта печи продолжительностью 8 ч или при простое более 2-3 ч по другим причинам низколегированную сталь разрешается выплавлять только после проведения одной — двух плавок углеродистой стали.
Шихтовка. Правильная шихтовка имеет большое значение для производительности печи и нормального хода плавки, а следовательно, и для качества выплавляемой стали. В составе железо-стальной части должно быть минимальное количество скрапа и стружки, во всяком случае не более 5 % каждого. Не допускается применять отходы, содержащие цинк, олово, свинец, сурьму и т. д. В свое время относительно высокому содержанию марганца в передельном чугуне придавали большое значение. Однако рядом работ, в частности работами Н. Н.Доброхотова и его школы, было показано, что как при скрап-процессе, так и при скрап-рудном процессе работа на маломарганцовистом чугуне имеет ряд экономических преимуществ: производительность печи повышается, а качество стали не понижается. Сказанное в еще большей степени относится к мартеновским печам, работающим, как правило, с интенсификацией окисления углерода при высоком температурном режиме на малосернистом коксовом или природном газе.
Переход на маломарганцовистый чугун при скрап-рудном процессе не влияет на условия десульфурации ванны в период доводки и на удаление фосфора в процессе шлакообразования.
Установлено, что применение маломарганцовистого чугуна и ведение плавки скрап-процессом без присадки ферромарганца не ухудшают качества стали, сокращают длительность плавки, снижают удельный расход марганца и уменьшают стоимость стали. При выплавке медь- и никельсодержащих сталей в завалку рекомендуется давать отходы никель-и медьсодержащей стали из расчета ввода в шихту до 0,5-0,6 %.
Следует отметить, что повышение тепловой мощности современных мартеновских печей, высокий температурный режим, при котором ведется плавка, а также продувка металла кислородом или компрессорным воздухом заметно облегчают условия передела шихты, содержащей до 1 % Сr. В этих условиях возможен также нормальный мартеновский передел шихты с более высоким содержанием хрома. Это было подтверждено исследованиями С. И. Собкина и И. М. Лейкина по переделу шихт с весьма высоким содержанием хрома (свыше 1 %) в мартеновской печи с продувкой ванны кислородом.
Преимущество применения агломерата и брикетов в дальнейшем получило широкое развитие. Одним из важных преимуществ применения офлюсованного агломерата или брикетов является возможность замены ими высококачественной железной руды. В завалке разрешается часть железной руды или брикетов (до 30%) заменить прокатной окалиной.
Завалка. Период завалки оказывает важное влияние на ход плавки. Послойная завалка известняка обеспечивает его лучшее взаимодействие с железной рудой и ускоряет процесс формирования шлака. При прогреве сыпучих не следует допускать оплавления руды и сыпучих, так как это приведет к удлинению периода плавления. При интенсивной подаче кислорода перерыв в завалке для прогрева сыпучих не требуется. Не рекомендуется вводить в завалку боксит, так как он увеличивает количество шлака и снижает его основность. Для ускорения перехода извести в шлаковый расплав нужно создать условия для хорошего ее контакта с оксидами железа. Этому может содействовать использование в завалке рудно-известняковых брикетов. Завалку следует форсировапть всемерно сокращая ее продолжительность. Для этого рекомендуется завалку производить двумя завалочными машинами. Заливка чугуна производится форсированно после прогрева шихты. Длительная заливка чугуна отрицательно сказывается на шлаковом режиме в период плавления И увеличивает общую длительность плавки.
Плавление. После выпуска необходимо следить за шлаком в печи и своевременно вводить соответствующие добавки. За 15-30 мин до полного расплавления определяют содержание углерода, серы и фосфора в металле. Если содержание углерода перед концом расплавления ниже предела, установленного для стали данной марки, разрешается до начала полировки долить жидкий чугун в количестве, обеспечивающем нормальное проведение периода чистого кипения.
Доводка. Полировка. В период полировки следует навести шлак нужного состава, закончить десульфурацию металла при энергичном окислении углерода. В этот период необходимо присаживать железную руду или другие окислители, количество которых определяется содержанием углерода в металле и температурой последнего. Количество железной руды, добавляемое в этот период, должно быть не менее 5 %. При работе с продувкой ванны твердые окислители при полировке могут не применяться. Для максимального удаления серы и фосфора выпуск шлака следует производить через 5-10 мин после ввода в печь окислителей. Шлак удаляется либо самотеком, либо принудительно мульдой завалочной машины без прекращения поступления в печь топлива. После скачивания шлака, в случае необходимости, производят дальнейшую полировку ванны рудой и одновременно присаживают кусковую известь, боксит или отходы корундового производства, шамот. Наводку шлака рекомендуется производить заранее приготовленной шлаковой смесью. Для интенсификации процесса десульфурации, при необходимости, можно в шлак добавить плавиковый шпат. Шлакообразующие следует вводить постепенно, по мере их усвоения, чтобы не замедлить процесс выгорания углерода и нагрева ванны. Для ускорения наводки шлака рекомендуется применять окалину. Известь следует применять свежеобожженную.
Боксит применяют сухим. Процесс дефосфорации должен обеспечить содержание в металле перед раскислением не выше 0,01-0,012% Р, так как в процессе раскисления стали содержание фосфора в металле заметно повышается из-за его восстановления из шлака.
Необходимо, чтобы основность шлака на протяжении периода доводки повышалась и к началу чистого кипения была не ниже 2,0—2,2. За период доводки основность шлака следует повысить не менее чем на 0,2-0,4. Показателем нормального проведения полировки является скорость выгорания углерода.
При выплавке никель- и медьсодержащих сталей для получения в металле заданного содержания никеля или меди в ванну после расплавления вводят расчетное количество металлического никеля, медьсодержащих отходов или металлической меди. Эти легирующие должны вводиться не позднее чем за 1,0-1,5 ч до выпуска плавки при условии нормального хода ее, в частности по содержанию серы. В случае необходимости можно добавлять медь и никель, но не позднее чем за 20 мин до раскисления.
Чистое кипение. Началом периода чистого кипения в печах, работающих без продувки кислородом, считают энергичное кипение ванны ровным пузырем не менее чем на 2/3 поверхности под сформировавшимся и жидкоподвижным шлаком со значительно осевшей пеной. При работе с продувкой ванны началом чистого кипения считают образование жидкоподвижного шлака. В отдельных случаях при правильной шихтовке плавки и нормальном тепловом режиме интервал между концом периода плавления и началом чистого кипения может быть минимальным.
В период чистого кипения разрешается изменять состав шлака небольшими добавками шамота, плавикового шпата и, в крайнем случае, сухого боксита. Присадку руды или, что лучше, окалины в этот период разрешается производить небольшими порциями (не более 500-700 кг). Присадку окислителей и боксита надо прекратить не менее чем за 30 мин до начала раскисления. Для интенсификации окисления углерода в сталях, раскисление которых производят при содержании углерода в ванне ниже 0,12%, добавку окалины прекращают не позднее чем за 15 мин до начала раскисления. При выплавке стали ответственного назначения, например для электросварных труб высокого давления, корпусной стали и т. п., добавку железной руды или боксита в период чистого кипения производить не рекомендуется (чтобы не вводить дополнительное количество водорода). Лишь в крайнем случае при отсутствии плавикового шпата и высоком содержании в металле серы допускается пользоваться добавками боксита, активизирующими процесс десульфурации. Уровень содержания марганца по ходу чистого кипения не регламентируется, присадка ферромарганца не разрешается.
Вопрос об оптимальном содержании марганца по ходу мартеновской плавки был предметом широкого обсуждения. Многие полагали, что одним из необходимых условий получения стали высокого качества, в первую очередь с низким содержанием серы, является достаточно высокое содержание марганца в шихте и по ходу плавки, достигаемое присадкой ферромарганца (или марганцевой руды). Однако многочисленные исследования и анализ работы большого числа заводов позволили однозначно решить вопрос о технической и экономической нецелесообразности ведения мартеновской плавки с присадками марганца. Это относится к выплавке как кипящих, так и спокойных сталей (в том числе низколегированных) скрап-процессом и скрап-рудным процессом.
Н.Н.Доброхотов, А.Н.Морозов, В. И.Явойский и др. установили, что поддержание высокого содержания марганца добавками ферромарганца оказывает отрицательное влияние на качество стали, снижая скорость окисления углерода, повышая содержание в стали водорода (вследствие уменьшения интенсивности кипения) и ухудшая условия дефосфорации. Добавка марганца по ходу плавки из-за низкой степени усвоения его металлом несколько удорожает стоимость стали. С точки зрения качества стали, оптимальным является обеспечение такого теплового и шлакового режима, при котором по ходу чистого кипения обеспечивалось бы повышение содержания марганца в стали в результате восстановления его из шлака. Такое повышение содержания марганца в стали является одним из показателей нормального теплового и шлакового режимов плавки.
Основность шлака перед раскислением должна быть не ниже 2,2. Период чистого кипения проводится с энергичным окислением углерода. Ранее считали, что одним из условий, обеспечивающих получение стали высокого качества, является окисление углерода в период чистого кипения с умеренной скоростью. Позже стали вести плавку, включая и период чистого кипения, с высокой скоростью окисления углерода, что является одним из условий получения металла с низким содержанием водорода и серы (при условии, если эта скорость соответствует степени нагрева металла), не снижая ее к концу плавки.
Соблюдение правильного теплового режима является одним из важнейших условий получения стали высокого качества. Поэтому по ходу плавки систематически должна контролироваться температура металлической ванны (обычно термопарой погружения по расплавлении, в начале и по ходу чистого кипения и обязательно перед раскислением). Оптимальная температура металла перед раскислением устанавливается в зависимости от марки стали, метода раскисления, способа разливки и веса слитков. Химический состав плавки в период чистого кипения регулярно контролируется. Состав шлака (его основность) контролируется по расплавлении, в начале и в конце чистого кипения.
При срыве наварки подины или откосов, сопровождающемся резким повышением вязкости шлака, скачкообразным понижением скорости выгорания углерода, плавка должна быть переведена в другую менее ответственную марку стали.
Продувку ванны кислородом допускается заканчивать за 15—25 мин до раскисления, а для наиболее ответственных марок за 30-40 мин. Такое положение оказалось возможным в результате эволюции во взглядах на ход мартеновской плавки. Считалось, что при выплавке качественной стали продувка ванны должна прекращаться возможно раньше, желательно до начала чистого кипения.
Многочисленные работы по исследованию влияния этого фактора на качество стали показали допустимость интенсификации процесса окисления углерода продувкой ванны кислородом в течение значительной части периода чистого кипения. Исследования влияния различных режимов продувки мартеновской ванны на качество стали 09Г2 (лист 13-40 мм) и 14ХГС (лист 11-14 мм) показали, что в плавках с продувкой ванны кислородом содержание азота в металле перед раскислением оказалось несколько более низким (0,0038 %), чем в сравнительных плавках с подачей кислорода только в факел. Было также показано, что продолжительность после продувочного периода в 15-20 мин обеспечивает снижение избытка кислорода в металле перед раскислением до уровня, который характерен для этих же марок стали, выплавленных с подачей кислорода только в факел.
Установлено, что при снижении продолжительности после продувочного периода с 55 до 15 мин содержание устойчивых неметаллических включений в металле перед раскислением даже несколько снижается, а общее их количество практически остается на одном уровне. Механические свойства листов, полученных из плавок, проведенных с различной удельной интенсивностью продувки (6,7-11,7 м3/(т-ч)), с различной продолжительностью после продувочного периода и с подачей кислорода только в факел, существенно не различаются.
Тоннаж мартеновских печей. Как уже указывалось, выплавка низколегированной стали большинства марок освоена в печах различного тоннажа, включая мощные печи — до 600 т (двухжелобные). В связи с этим был проведен ряд работ по сравнению качества стали, выплавленной в одно- и двухжелобных мартеновских печах. В работе было исследовано качество низколегированной стали разных марок, выплавленных в мартеновских печах емкостью 250 и 500 т. По содержанию в металле кислорода (при разливке) сталь, выплавленная в тех и других печах, оказалась практически одинаковой, однако количество неметаллических включений в большинстве случаев в металле из больших печей оказалось несколько меньше. Это, по-видимому, связано с относительно меньшей поверхностью соприкосновения металла со шлаком, а также с подом и откосами печи. Средние показатели характеристик прочности у металла из больших печей несколько ниже при практически одинаковых значениях пластичности и ударной вязкости. При выплавке низколегированной стали в 500-т печах не было отмечено ухудшения службы пода. Расходные коэффициенты при последующих переделах металла, выплавленного в 250-т и 500-т печах, оказались практически одинаковыми.
Было проведено сопоставление уровня механических свойств листовой стали марки 14ХГС, выплавленной в 300-т и 550-т печах. В малых печах было выплавлено 111 плавок (1 группа плавок), а в большегрузных — 88 (II группа). Средний химический состав I группы плавок был следующим: 0,133% С; 1,07% Мn; 0,563 % Si; 0,652 % Сr; 0,025 % Р; 0,0364 % S; II группы: 0,131% С; 1,05% Мn; 0,548 % Si; 0,636 % Сr; 0,029% Р и 0,0350% S. При выплавке стали в больших печах содержание марганца, кремния и хрома несколько ниже. Можно полагать, что это связано с большим количеством шлака, остающегося в большегрузных печах к моменту раскисления, и более низкой его основностью. Известную роль играет также увеличение времени выпуска плавки из большегрузных печей, когда особенно интенсивно развиваются реакции вторичного окисления. По указанным причинам угар элементов в процессе предварительного раскисления металла в печи и выпуска плавки в больших печах будет выше, чем в малых. Эти же факторы влияют на несколько более высокую степень восстановления фосфора в больших печах в процессе раскисления.
Качество низколегированной стали, выплавленной в печах различной емкости (до 600 т), практически одинаково.
В последние 30—40 лет в России разработаны процессы интенсификации выплавки мартеновской стали продувкой ванны кислородом. Однако при этом значительно повышается температура отходящих газов. В этот же период были сконструированы и построены в существующих мартеновских цехах двухванные печи. Технология выплавки стали в двух-ванных и обычных мартеновских печах практически не отличаются, однако технико-экономические показатели и эффективность производства металла массового назначения в двухванных печах значительно выше.
Особенностью конструкции двухванных печей является то, что они позволяют утилизировать тепло как отходящих газов, так и выделяющееся при окислении СО.
Утилизация тепла, выделяющегося в соседней ванне, позволяет на 7-15 % снизить расход чугуна, заменив его стальным ломом.
Некоторые технологические параметры выплавки стали. Наиболее важной задачей при выплавке стали в мартеновских печах является удаление из металла фосфора, серы и неметаллических включений.
Как правило, принимаются меры по снижению содержания фосфора уже на первых стадиях процесса — во время плавления и в начале периода кипения, т.е. при умеренных температурах металла. Для эффективного удаления фосфора, кроме умеренной температуры, необходимо, чтобы железистоизвестковый шлак имел высокую основность. В этом случае резко снижается активность прочных соединений фосфора в шлаке, и он удаляется из ванны при скачивании шлака. Если сталь выплавляется на ломе, состоящем из отходов собственного производства, то для обеспечения в расплаве содержания фосфора на уровне 0,010-0,015 % достаточно скачать шлак один раз. Однако иногда, чтобы получить такое содержание фосфора, бывает необходимо скачивать и наводить новый шлак до трех раз.
Для эффективного удаления серы из металла шлак должен иметь высокую основность, что достигается периодическими присадками извести, развитой поверхностью соприкосновения с металлом, что обеспечивается энергичным перемешиванием ванны, периодическим скачиванием шлака и наведением нового. Для выплавки мартеновской стали с относительно низким содержанием серы следует использовать низкосернистые энергоносители. Наиболее предпочтительным является природный газ. Мазут и коксовый газ должны подвергаться очистке с целью снижения в них содержания серы.
При выплавке мартеновской стали большое внимание уделяется основному периоду процесса — кипению ванны. Период кипения характеризуется окислением (выгоранием) содержащегося в металле углерода до его газообразного соединения СО. В процессе кипения ванны происходит удаление из расплава газов — кислорода, азота и водорода. При этом азот и водород диффундируют в пузырки СО, одновременно (вместе) сними всплывают и уносятся под свод печи. Во время кипения увеличивается поверхность контакта металла со шлаком, неметаллические включения укрупняются, всплывают, переходят в шлак и удерживаются им.
В ходе освоения производства низколегированной стали для газопроводных труб исследовали влияние отдельных параметров технологии производства на механические свойства листовой стали и, в первую очередь, на уровень пластических и вязких свойств. Эту зависимость устанавливали статистической обработкой технологических (паспортных) данных и результатов сдаточных испытаний листовой стали. Полученные результаты по 2000 плавок некоторых марок низколегированной стали выплавленных в 250-300-т и 500-550-т мартеновских печах приведены ниже.
Изменение технологических параметров в исследованных пределах не оказало заметного влияния на характеристики прочности. С точки зрения уровня пластических и вязких свойств, оптимальными параметрами плавки стали 14ХГС в 550-т печах одного из заводов без продувки ванны кислородом являются содержание углерода по расплавлении 0,5—0,8 % и перед раскислением 0,07-0,1 %; основность шлака по расплавлении не менее 1,6 и перед раскислением не менее 2,2; максимально высокая скорость окисления углерода в период чистого кипения; продолжительность предварительного раскисления в печи не более 40 мин и выпуска не более 25 мин. Не установлено сколько-нибудь заметного влияния остальных исследованных параметров выплавки на механические свойства нормализованных листов из стали 14ХГС. Механические свойства листов, прокатанных из металла первых и вторых ковшей, оказались практически одинаковыми.
Для условий другого завода при выплавке стали марки 17ГС в 550-т печах оптимальными параметрами выплавки и разливки стали, с точки зрения уровня пластических и вязких свойств горячекатаных листов толщиной 7,5-8,0 мм и качества поверхности слябов и листов, оказались следующие: содержание углерода по расплавлении в пределах 0,6-0,9 %, особенно нежелательно «крепкое» расплавление (>1,0% С), и возможно низкое содержание серы по расплавлении, желательно не выше 0,4 %.
Не отмечено влияние Содержания углерода перед раскислением на ударную вязкость. С увеличением в этот период содержания углерода несколько понижается относительное удлинение. Это, очевидно, связано с более высоким содержанием углерода и марганца в готовой стали таких плавок, что подтверждается более высокими прочностными характеристиками листов этой группы плавок. Влияние указанного фактора на качество поверхности слябов и листов не отмечено. Минимальная ударная вязкость наблюдалась в металле плавок с продолжительным периодом чистого кипения (более 80 мин).
По уровням относительного удлинения и ударной вязкости стали следует отдать предпочтение плавкам, период раскисления которых не превышал 15 мин. Для плавок этой группы получено и лучшее качество поверхности листов.
Не установлено четкого влияния основности шлака по расплавлении на относительное удлинение. Оптимальную ударную вязкость имела сталь плавок, основность шлака которых по расплавлении составляла 1,7-1,9, перед раскислением — не менее 2,5. Известное влияние на свойства стали оказывают не только абсолютные значения основности шлака, но и ее приращение в период между расплавлением и раскислением. Желательно, чтобы приращение основности за рассматриваемый период было не менее 0,3—0,4. Этот фактор благоприятно влияет как на ударную вязкость листов, так и на качество их поверхности.
Не установлено связи между содержанием FeO в шлаке перед раскислением, а также продолжительностью чистого кипения без присадки окислителей и относительным удлинением и ударной вязкостью, а также качеством поверхности листов.
С повышением температуры металла перед раскислением увеличивалась ударная вязкость, улучшалось качество поверхности листов и снижался расходный коэффициент. При этом несколько увеличилось количество слябов, требовавших глубокой вырубки (зачистки). Дальнейшее, сверх 1610° С, повышение температуры металла перед разливкой сверху привело к понижению ударной вязкости.
Использование при разливке сверху ковшей с двумя разливочными стаканами сокращает время разливки и обеспечивает более высокую температуру разливки второй половины плавки. Ударная вязкость листов, полученных из плавок, разлитых через двухстопорный ковш, оказалась несколько выше. Для металла этих плавок характерно также несколько меньшее количество испытаний, при которых относительное удлинение было ниже 24 %, и несколько большее — с ударной вязкостью при -40° С ниже 40 Дж/см2.
При составлении основных положений технологии производства низколегированной стали необходимо базироваться на данных, полученных при указанных статистических обработках.
Выплавка стали
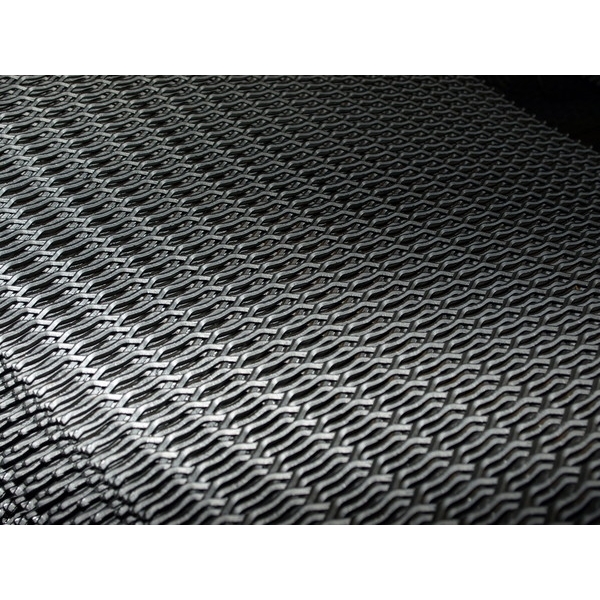
- 05/12/2013
- 7316 views
Мартеновское производство